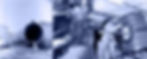
ABOUT US
We are suppliers of fuel cells and flexible liquid storage equipment for defense and commercial industries.
Our Story
On November 30, 2018, LB Advisors and Jet Capital created an entity named LB Amfuel which purchased the assets of the old Amfuel out of bankruptcy with the intention of returning it to a growth phase. The majority of Amfuel’s production is for the U.S. Department of Defense and foreign allies.
Amfuel has two facilities in Magnolia, Arkansas, located on 78 acres, with 355,000 square feet of production area. Amfuel employs over 300 workers with over 60 years of experience in the production of coated fabric products and aviation fuel cells.
Quality Standards
Amfuel is qualified for the following products and services: The design and manufacture of aircraft fuel cells for fixed-wing and rotary aircraft; missiles; ground vehicles; truck mounted tanks, embankment supported tanks, dunnage bags and other coated fabric items.
Amfuel’s quality policy ensures complete customer satisfaction. Every level from management to production is involved in quality control to assure our customers receive the highest standards of product integrity and safety.
Design
Amfuel’s design and engineering departments have developed a wide range of products based upon extensive training in the complex assembly of elastomers, metals, plastics, fabrics, films, and adhesives.
With a high level of commitment to cutting-edge technology, Amfuel continues to expand its product line for military and commercial use.
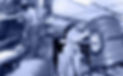
Stats
Sitting on
78 Acres
Operation
355,000 Square Ft.
Employs Approx.
300+ Employees
Experience
60+
Years
Manufacturing Capabilities
Fuel Cells
History
In 1941, Ernst Eger patented a self-sealing fuel tank design for United States Rubber Company (later Uniroyal),, one of many companies involved in developing this technology during WWII A Goodyear chemist, James Merrill, filed a patent in 1941 (published in 1947) for refining and successfully testing his method for manufacturing self-sealing tanks using a two-layer system of rubber compounds encased in a metal outer shell or the wing lining of the aircraft. By 1942, fireproof tanks had developed the first flexible fuel bladders as range extender tanks for the MkIX Spitfire. These tanks were flexible containers, made of a laminated self-sealing material like vulcanized rubber, and with as few seams as possible to minimize leak paths.
Not all fighters were fitted with the relatively new invention. Self-sealing tanks tended to be heavier and of lower capacity than non-sealed tanks. Nonetheless, aircraft that were fitted with self-sealing tanks regularly took more punishment than those without and were able to return to base. Combat experience in the Pacific showed that the heavily protected American aircraft could sustain far more damage than the lightly armored Japanese designs without self-sealing fuel tanks (for instance, the Mitsubishi A6M Zero).
Modern Use
Most jet fighters and all US military rotary wing aircraft have self-sealing tanks. Military rotary wing fuel tanks have the additional feature of being crashworthy. High altitudes require the tanks to be pressurized, which makes self-sealing difficult. Newer technologies have made advances like inert foam-filled tanks to prevent detonation. This foam is open cell foam that effectively divides the gas space above the remaining fuel into thousands of small spaces, none of which contain sufficient vapor to support combustion. This foam also serves to reduce fuel slosh.
For military use, tanks are qualified to MIL-DTL-27422 (includes crashworthiness requirements) or MIL-DTL-5578 (non-crashworthy). An aircraft fuel tank sometimes consists of several interconnected fuel cells. The interconnecting hoses are typically also self-sealing.
In addition to fighter aircraft and rotorcraft, some military patrol vehicles and armored VIP limousines feature self-sealing fuel tanks. Self-sealing fuel tanks using military technology are also required in some motorsport categories.